Bigger isn’t always better, but in construction the size of a company can significantly influence its ability to manage safety effectively. Small businesses, particularly those with between one and ten employees, often face unique challenges that predispose them to higher risks of fatal falls and other severe accidents.
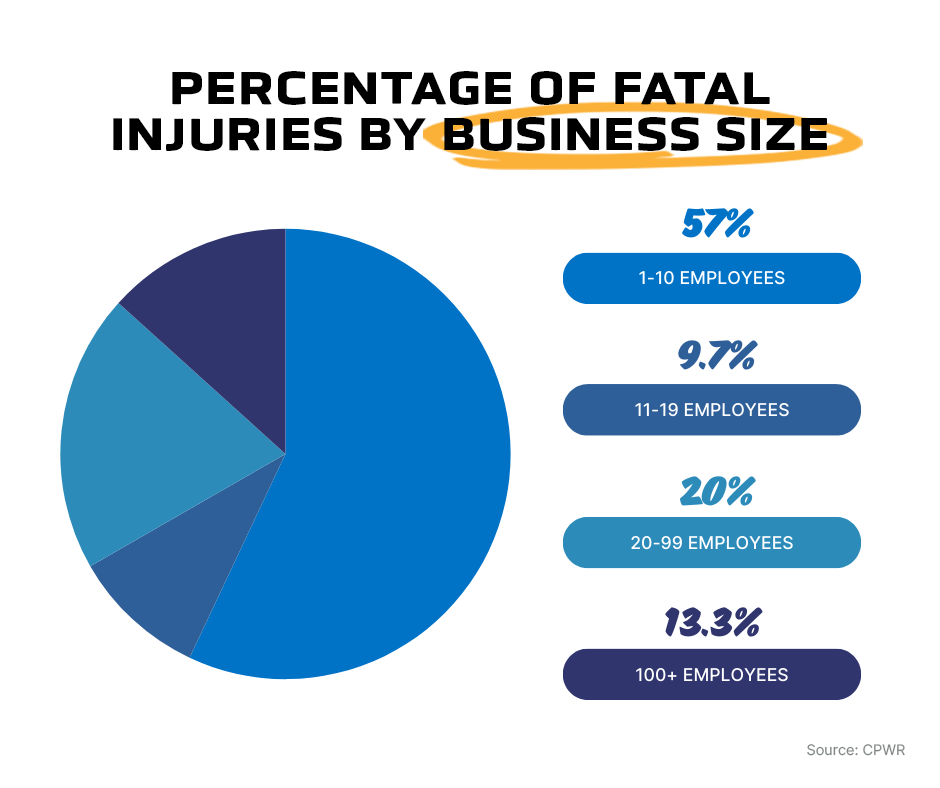
So why do small construction businesses account for 57% of fatal injuries and more than 70% of fatal falls? Much of it is due to the “just-get-it-done” culture in small businesses, resource limitations, and budget constraints. If any of that sounds familiar, read on to understand how cutting safety corners could result in significant financial losses and, more importantly, the loss of lives.
Safety and Small Construction Businesses: 5 Troubling Statistics
- From 2011 to 2022, 5,400 employees of small businesses were the victims of fatal injuries.
- While about 9 out of 10 businesses with 500 or more employees adopt safety practices involving PPE, only 55% of businesses with less than 10 employees used PPE.
- Small businesses pay more in OSHA fines (77%) than the largest businesses (11%).
- Only 34.5% of near-misses are taken seriously and investigated by businesses with less than 10 employees.
- Only 35.5% of small construction businesses conduct regular health and safety training, and only train when hiring or when required.
Limitations and Challenges that Impact Safety in Small Businesses
Small construction businesses face unique challenges that significantly impact workplace safety. Limited resources, insufficient training, regulatory compliance difficulties, and overlapping roles all contribute to heightened risks and potential hazards on the job site.
Limited Resources: Small firms typically operate with tighter budgets, which can restrict their ability to invest in the best safety equipment and training programs. The cost of cutting-edge harnesses, scaffolding, and other safety measures can be prohibitive, leading to the use of less effective alternatives.
Insufficient Safety Training and Awareness: Comprehensive safety training requires both time and money, resources that are in short supply in many small businesses. This often results in inadequate training on safety protocols and the proper use of equipment.
Regulatory Compliance Difficulties: While all construction firms must comply with occupational safety and health regulations, smaller firms might struggle with the complexity and breadth of these requirements due to less access to expert guidance within their staffing constraints.
Overlapping Roles: In small firms, employees often wear multiple hats, performing tasks beyond their primary expertise. This versatility, while a strength in some respects, can lead to situations where workers engage in tasks without adequate safety knowledge or preparation.
The Safety Culture in Small Teams Puts People at Risk
The culture within a small business can significantly impact its safety outcomes. In a tight-knit team, workers might feel pressure to skip safety measures to meet deadlines or keep costs down, especially when directed by someone they know personally, like a small business owner.
Smaller teams are more likely to use informal communication — where a business with 70 employees would send an email to get everyone on the same page, a team of 7 can get by with word-of-mouth. While less formal communication channels can be a benefit in some areas, they can also lead to misunderstandings or under-communication about safety needs and protocols.
Workers may also hesitate to report minor incidents or near-misses, fearing repercussions in their close-knit work environment or not wanting to cause financial strain by halting a project.
The Cost of Cutting Corners
In the last decade, small construction businesses accounted for between 73% and 78% of all of the OSHA citations. While the number of citations has dropped significantly since 2013, there is still an average of nearly 40,000 citations per year.
For serious and other-than-serious violations, the maximum OSHA penalty is $16,131 USD per violation, with the minimum serious penalty being $1,190 per violation. The statutory minimum penalty for a willful violation—where the employer knew that a hazardous condition existed but made no reasonable effort to eliminate it— is $11,524 USD.
The National Safety Council (NSC) estimates that the average cost of a workplace fatality exceeds $1 million, considering direct and indirect costs such as legal fees, lost productivity, and insurance premiums. For small businesses, these costs could be devastating.
From 2011 to 2022, 5,400 employees of small businesses in the U.S. were the victims of fatal injuries— that’s almost 500 deaths per year. It’s also more than 23x the amount of people who died while working for larger companies with more than 100 employees.
The reality is that small construction businesses are falling behind the larger firms in safety management and safety culture measures, including:
- Using personal protective equipment (PPE)
- Inspecting equipment for functionality prior to use and installing safety protections
- Developing specific health and safety plans
- Having measurable safety goals and objectives
- Establishing site specific training programs
- Offering safety incentives
- Conducting regular safety training
According to the most recent study on the topic by The Center for Construction Research and Training in 2016, this is the breakdown:
4 Strategic Approaches to Enhancing Safety in Small Teams
For small construction businesses, improving safety is not just about compliance but about cultivating a culture that prioritizes worker well-being above all. Implementing the following strategies can make a significant difference:
- Regular and Rigorous Training: Invest in ongoing safety training tailored to the specific risks workers face on-site. Utilize online resources and local safety courses to keep training up-to-date and affordable.
- Invest in Quality Safety Equipment: Allocate budget towards high-quality safety gear and regularly maintain and update this equipment. It’s an upfront cost that saves you big in the long run, so consider
- Create a Safety-First Culture: Encourage open communication about safety concerns. Make it clear that safety takes precedence over speed or cost-saving.
- Leverage Software / Technology: Use project management and safety apps designed for small construction businesses to track safety compliance and training effectively.
How Construction Management Software Can Help Small Businesses
Aside from aiding the business in complying with OSHA’s recordkeeping and reporting requirements (which may or may not apply to some small businesses), implementing construction management software with a focus on safety management is a great way to keep both your workers and your business protected from fatal injuries and falls.
Here are three key ways it can help:
Enhance Safety Compliance and Accountability
Implementing software with features like certification management and digital inspection forms, you can ensure that all safety certifications are up to date and easily accessible. Expiry notifications prevent lapses in critical safety training, while e-signatures on safety forms create a verifiable record of compliance. This systematic approach to managing safety documentation helps small businesses maintain high safety standards and reduce the risk of fatal incidents.
Streamline Safety Inspections and Reporting
Digital inspection forms that can be filled out via QR code and mobile phone make it easy for field workers to conduct and document safety inspections in real-time. This not only saves time but also ensures that safety checks are consistently performed and recorded. Dashboards to track tasks and incomplete forms provide management with clear visibility into safety compliance, enabling proactive measures to address any gaps or issues.
Centralize Safety Data for Quick Access and Decision Making
Digital SDS binders and accessible project information, including safety policies, provide workers with instant access to critical safety data. This centralization of information means that, in the event of an emergency or safety concern, employees can quickly find and reference the necessary protocols and material safety data sheets (SDS), leading to faster, more informed decision-making and response.
By leveraging these capabilities, small construction businesses can significantly improve their safety management practices, reducing the likelihood of fatal injuries and falls, and fostering a safer work environment for their employees.
Ensuring Safety and Compliance in Small Construction Businesses
According to U.S. Census data, in 2013, the total number of construction workers employed in businesses with fewer than 10 employees was almost 2 million (1,873,475). Over a decade later, that number has likely grown significantly.
Did you know that when an OSHA representative asks for specific records, you must provide copies within four (4) business hours? For small construction businesses, this can be a daunting task. Do you think you could locate the necessary documentation related to an incident or violation within that critical four-hour window?
Implementing construction management software can help streamline document management, ensuring all records are easily accessible and organized. This not only aids in compliance but also reinforces a culture of safety. By understanding the unique challenges small construction businesses face and adopting strategic safety practices, the risk to workers can be significantly mitigated. Building a culture that emphasizes safety can protect lives and ensure that small businesses not only survive but thrive in the competitive construction industry.